MarineDrives
Marine Drives
AAmpere (amp), SI unit of electrical current standard marine drive system consists of an engine, reduction gear, propeller shaft and bearings, and a propeller. Alternate drives consist of an engine, hydraulic pump or alternator, shaft motor (hydraulic or electric), propeller shaft and bearings, and a propeller.
Mechanical Drives
Hard Mounts
In a standard mechanical-drive system, the engine is hard mounted to the engine bed because the propeller thrusts the engine A reduction-gear transmission such as ZF reduces the engine rpmRevolutions per minute to the rpm required by the propeller. The propeller shaft is fixed, and great care is taken to align the shaft with the engine. Periodic re-alignment may be necessary.
The advantages are simplicity, low cost, reliability, ease of repair, and maximum mechanical efficiency of around 95%percent.
The disadvantages are increased noise and vibration, central engine-room placement, and stress on the engine. Noise and vibration are transmitted directly through the hull. To get the right angle on the propeller shaft, the engine room usually has to be placed amid-ships. Finally, the thrust of the propeller pushes directly against the engine.
Constant Velocity
In a constant-velocity (CVConstant velocity) anti-vibration system such as the AquaDrive®,[1] there is a propeller shaft and a separate drive shaft, coupled with a CV joint. The propeller shaft ends in a thrust bearing mounted to the hull.
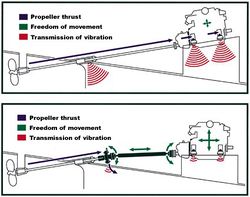
This bearing takes the end-thrust from the propeller and transmits it to the hull to move it through the water. The drive shaft has a CV joint at both ends, and is splined inside so that its length is adjustable. This allows the engine to be mounted on flexible rubber mounts.
The advantages are reduced noise and vibration, slightly more flexibility in the placement of the engine, and no stress on the engine.
The disadvantages are higher cost, higher maintenance due to the CV joints, and increased complexity of repair. But don’t take this too much to heart. CV joints are in most cars, trucks, buses, tractors and racecars.
Other noise-reducing systems include the Centaflex AGMAbsorption glass mat[2] and Rubber Design.[3]Mechanical VVolt-Drive
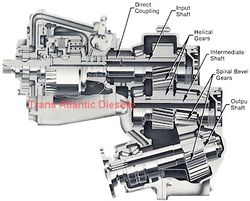
A mechanical V-drive is a compact reduction-gear transmission that reverses the direction of the drive shaft. It allows the engine to be placed aft, facing aft, with the output shaft facing forward. The V-drive reverses the direction of the output to connect to the propeller shaft, usually at an angle of 10-15 degrees. Typical manufacturers are: Borg Warner, Halibrand, Twin Disc Marine Transmis-sions, Yanmar, and ZF.
With a V-drive, there is no reason not to have the engine room fully aft, taking full advantage of the forward hull for accommodation.
Non-Mechanical Drives
Hydraulic Z-Drive
A hydraulic Z-drive such as the Thrustmaster[4] or Olympic[5] is the next step up from a V-drive. In this layout, the engine drives a hydraulic pump. This connects to a hydraulic shaft motor via hydraulic lines. The shaft motor turns the propeller shaft. Typically, the shaft and propeller are mounted so that the propeller can swivel through 360 degrees.
Thus, a Z-drive removes the need for stern thrusters. The engine does not have to be inline, and can be put anywhere convenient. Z-drives allow the engine room to be aft.
There is a bias against hydraulic drives because of their additional complexity, and perceived lack of efficiency and robustness. Hydraulic systems lose energy mainly through torque losses, and are typically 80-85% efficient. This is not quite as efficient as a straight mechanical or an electrical drive. If you have doubts about robustness, go watch some heavy equipment in operation. Z-drives of 4,000-hphorsepower and up are routinely fitted to tugs. The only thing against hydraulic drives is their cost.
Azipod®
An Azipod®[6] (azimuth thruster) is a form of rudderless diesel-electric propulsion. They were developed in 1990 by ABB Group, primarily to drive large cruise ships. A pod combines the main electric drive motor and propeller in a casing beneath the ship. Typically the propeller is on the front of the pod. The pod rotates through 360 degrees, providing steering, stern thrusting and reversing.
Like other forms of diesel-electric propulsion, pods reduce fuel consumption because the diesel generator runs at an optimum fixed speed. Turning circles are reduced by as much as 30%.
Pods have also been designed with contra-rotating propellers, one at the front and one at the rear of the pod, to further increase fuel efficiency. Pods have since been used on icebreakers like the USCG Mackinaw and on cargo ships. Robust pods have been developed for icebreakers with strengthened propellers to chop the ice. And pods are starting to appear in larger yachts.
Diesel-Electric
Diesel-electric propulsion systems are not new. They have been used in submarines, trains and buses. In a diesel-electric system, the engine drives a high output DCDirect current generator. The current from this drives one or more electric motors connected to the propeller shaft. The chief advantage of an electrical drive is increased performance throughout the speed range. This results because the engine can be run at its optimum RPM, while the speed of the boat is regulated by the electrical drive.
Much is said about the higher efficiency of mechanical drives, but electric drives are more or less as efficient as mechanical ones. The efficiency of an electric motor is measured in Watts-out/Watts-in, where Watts out are measured in hp x 746. Generally, modern electric motors (NEMA standard) have an efficiency between 87 and 97%, with larger motors being more efficient. Overall the efficiency will run around 81%, assuming the electrical generator converts 90% of the diesel engine'sSecond output into electrical energy and the traction motors convert 90% of this electrical energy back into mechanical energy on the propeller shaft.
Relevant standards are IEEE 112, JEC 37, and IEC 34-2. The main energy loss in electric drives is through energy transformed to heat.[7][8]
Diesel-electric drives seem to have evolved at different times in different sectors. Rudolf Diesel, a refrigeration engineer, invented and developed the diesel engine between 1893-97.[9] In World War I, British C-Class submarines in 1906 were gasoline-electric. The DDisplacement, Depth of ship-Class, in 1908, introduced diesel-electric.[10] In the railroad sector, in the United States, General Electric introduced gasoline-electric locomotives in 1913, switching to diesel in 1917.[11]
Electric drives are very reliable, with a MTBF of 25,000 hours (about 2.8 years of continuous running). Brushless (permanent magnet) motors are more robust and are becoming cheaper as patents expire. Commercial trawler systems such as FEYS are warranted for 10,000 hours (1.1 continuous years). Some other factors to consider are lower noise and fuel consumption, and costs.[12]Continuously Variable Transmission
Continuously Variable Transmissions (CVTContinuously variable transmission) are mentioned here only for completeness. A CVT has a nearly infinite range of gear ratios. Like a controllable-pitch propeller, a CVT allows the engine to operate at its optimum rpm regardless of the speed. Until recently, CVTs were too expensive and unreliable for use in cars; although hydrostatic types have been used in main battle tanks. They are unlikely to be adapted for marine use.
References
- ↑ AquaDrive, http://www.aquadriveusa.com/advantage/advantage.htm
- ↑ CENTA, http://www.centa-uk.co.uk/
- ↑ Rubber Design, http://www.rubberdesign.nl/
- ↑ Thrustmaster of Texas, Inc., http://www.thrustmastertexas.com/
- ↑ Summer Equipment, Olympic Steerable Drive, http://www.summerequipment.com/
- ↑ Azipod® is a registered trademark of the ABB Group
- ↑ AC Motor Efficiency Guide, Rockwell Automation, http://www.reliance.com/mtr/b7087_5/b7087_5_3.htm
- ↑ Advanced Energy, http://www.advancedenergy.org/progressenergy/motor_efficiency.html
- ↑ About, http://inventors.about.com/library/inventors/bldiesel.htm
- ↑ Royal Navy Submarines (D-Class 1908 to 1911), http://members.iinet.net.au/~eadej/dclass.html
- ↑ The Evolution of the Diesel Locomotive in the United States, Benn Coifman, 1994, the yardlimit
- ↑ FAST Electric Yacht Systems, Inc., http://www.feys.org/